We use cookies to make your experience better. To comply with the new e-Privacy directive, we need to ask for your consent to set the cookies. Learn more.
Parts On Demand
High Performance Plastics
Rubber-65A BLK

Material Overview
Rubber-65A BLK is a mid-tear strength, high elongation at break and Shore 65A hardness material. It allows for production of medium hard rubber parts with slow rebound.
Common Applications
Rubber-65A is ideal for applications such as grips, handles, gaskets, bumpers, seals, vibration dampening components and more.
Key Material Properties
High Elongation at Break
Environmental Stability
Shore-A 65 Hardness
Elongation at Break % 126
Tensile Modulus 23 MPa
Shore Hardness 65 A
Tear Strength ISO 34-1 Type C – 8.5 kN/m, Type T – 1.8 kN/m
Maximum Part Size 124.8 x 70.2 x 196 mm (4.9 x 2.8 x 7.7 in)
Layer Thickness Options 10, 20, 30, 40, 50, 100 Micron Layers
What is the 3D printing process for this material?
Rubber-65A is printed utilizing 3D Systems' Figure 4 DLP (digital light processing) 3D printing technology. The Figure 4 is a high-speed 3D printer that offers the quality and performance of injection-molded parts with smooth surface finish and exceptional sidewall quality, without the time or cost of tooling.
Will there be support scarring on this part?
The figure 4 material utilizes small supports similar to stereolithography (SLA). When removing the support structure duing post processing, small nubs will remain on the part. it is important to identify the class A surface of the part before printing to ensure that the small support nubs do not touch the crititcal surface of the part.
How long will it take before I receive my part in this material?
Production times vary depending on machine availability, but generally Rubber-65A parts are printed and shipped within 2-3 business days.
What are some of the specific design considerations when designing parts for this material?
The design considerations recommended for Rubber-65A are similar to those recommended for any photopolymer 3D printing technology. You will want to give thought to the kinds of design considerations and fundamental ranges of capability that apply for any manufacturing device, such as minimal wall thicknesses and things of that nature, which tend to vary from geometry to geometry and part to part. Often the best way to determine the functional range for a specific application is to print it and test it. Iterate out all the opportunities for manufacturing efficiencies before you scale up to high volume production.
Upload A File To Get Started
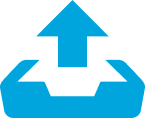